Induction Melting Machines
As manufacturer of induction melting furnaces, Hasung offers a wide range of industrial furnaces for the heat treatment of gold, silver, copper, platinum, palladium, rhodium, steels and other metals.
The desktop type mini induction melting furnace is designed for small jewelry factory, workshop or DIY home use purpose. You can use both quartz type crucible or graphite crucible in this machine. Small size but powerful.
The MU series we offer melting machines for many different demands and with crucible capacities (gold) from 1kg up to 8kg. The material is molten in open crucibles and poured by hand into the mould. These melting furnaces are suitable for melting gold and silver alloys and as well as aluminium, bronze, brass a.s.o. Due to the strong induction generator up to 15 kW and the low induction frequency the stirring effect of the metal is excellent. With 8KW, you can melt platinum, steel, palladium, gold, silver, etc. all in 1kg ceramic crucible by changing crucibles directly. With 15KW power, you could melt 2kg or 3kg Pt, Pd, SS, Au, Ag, Cu, etc. in a 2kg or 3kg ceramic crucible directly.
The TF/MDQ series melting unit and crucible can be tilted and locked in position by the user at multiple angles for gentler filling. Such “soft pouring” also prevents damage to the crucible. Pouring off is continuous and gradual, using a pivot lever. The operator is forced to stand to the side of the machine – away from the dangers of the pouring off area. It's the most safe for operators. All the axis of rotation, handle, position for holding mould are all made of 304 stainless steel.
The HVQ series are the special vacuum tilting furnace for high temperature metals smeltingsuch as steel, gold, silver, rhodium, platinum-rhodium alloy and other alloys. Vacuum degrees could be according to customers' requests.
-
Hasung-30kg, 50kg Automatic Pouring Melting Furnace
The equipment adopts tilting type independent handle pouring operation, convenient and safe pouring, the maximum temperature can reach 1600 °C,With Germany lGBT induction heating technology, rapid smelting of gold, silver,copper and other alloy materials, the whole smelting process is safe to operate,when the smelting is completed, only need to pour liquid metal into the graphite mould with handle without press “Stop” button, the machine stops heating automatically. -
Hasung-Digital Induction Melting Furnace
The equipment adopts Germany lGBT induction heating technology, which is safer and more convenient. The direct induction of metal makes the metal basically zero loss. lt is suitable for the smelting of gold, silver and other metals. Cooling water circulation treatment system, integrated self-developed induciton heating generator,intelligent powersaving, high output power.Good stability.
-
Small Metal Induction Melting Furnace 3kg 4kg
Capabilition of 3kg or 4kg gold capacity, small size, fast melting.
Available for gold, karat gold, silver, copper, alloys, etc.
Compact size, unique design
Suitable for jewellers, DIY workshop, small metal goldsmith.
-
Platinum Induction Melting Furnace 1kg 2kg 3kg 4kg 5kg Hasung
Equipment Introduction:
This device uses high-quality German IGBT module heating modules, which are safer and more convenient. The direct induction of metal reduces losses. Suitable for the melting of metals such as gold and platinum. Hasung’s independently designed and developed heating system and reliable protection function make the entire machine more stable and durable.
-
Tilting Induction Melting Furnace For Gold Platinum Palladium Rhodium 1kg 2kg 3kg 4kg 5kg 6kg 8kg
The design of this tilting melting system is based on the actual needs of the project and process, using modern high-tech technology. Safety guarranted.
1. Adopt German high-frequency / Low Frequency heating technology, automatic frequency tracking and multiple protection technology, which can melt metals in a short time, save energy and work efficiently.
2. Using electromagnetic stirring function, no segregation in color.
3. It adopts Mistake Proofing (anti-fool) automatic control system, which is easier to use.
4. Using PID temperature control system, the temperature is more accurate (±1°C) (optional).
5. The HS-TFQ smelting equipment is independently developed and manufactured with advanced technical level products for the smelting and casting of gold, silver, copper, etc.
The HS-HS-TFQ series is designed for melting platinum, palladium, Rhodium, gold, silver, copper and other alloys.
6. This equipment apply many foreign famous brands components.
7. It keeps heating while pouring metal liquids at a great condition which enables users to get great quality casting.
-
Rotary Vacuum Induction Melting Furnace (VIM) FIM/FPt (Platinum, Palladium Rhodium and Alloys)
FIM/FPt is a vacuum furnace for melting platinum, palladium, rhodium, steel, and high temperature alloys with tilting mechanism.
It can be used to obtain a perfect melting of platinum and palladium alloys without any gas inclusions.
It can melt from a minimum of 500g to a maximum of 10kg of Platinum in minutes.
The melting unit is composed of a water-cooled stainless steel casing in which the case with crucible rotate and an ingot mold for tilting casting.
The melting, homogenization and casting phase can take place under vacuum or in a protective atmosphere.
The furnace is complete with:
- Double stage rotary vane vacuum pump in oil bath;
- High precision digital pressure sensor;
- Optical pyrometer for temperature control;
- High precision digital vacuum switch for vacuum reading + Display.
Advantages
- Vacuum melting technology
- Manual/Automatic tilting system
- High melting temperature
Hasung Technology High Temperature Vacuum Induction Melting Furnace Experimental Vacuum Melting Furnace
Product Features
1. Fast melting speed, the temperature can reach above 2200℃
2. With mechanical stirring function, the material is stirred more evenly
3. Equipped with programmed temperature control, set the heating or cooling curve according to your process requirements, the equipment will automatically heat or cool according to this process
4. With a pouring device, the molten sample can be poured into the prepared ingot mold, and the shape of the sample you want can be poured
5. It can be smelted under various atmosphere conditions: smelting in air, protective atmosphere and high vacuum conditions, buy one kind of equipment, realize various functions; save your cost to a certain extent.
6. With secondary feeding system: It can realize adding other elements during the melting process, which is convenient for you to prepare diversified samples
7. The furnace body is all stainless steel with water cooling to ensure that the temperature of the shell is lower than 35 °C to protect your personal safety
-
Tilting Induction Melting Machine For Gold Silver Copper 2kg 3kg 4kg 5kg 6kg
The design of this tilting melting system is based on the actual needs of the project and process, using modern high-tech technology. Safety guarranted.
1. Adopt Germany IGBT heating technology, automatic frequency tracking and multiple protection technology, which can melt metals in a short time, save energy and work efficiently.
2. Using electromagnetic stirring function, no segregation in color.
3. It adopts Mistake Proofing (anti-fool) automatic control system, which is easier to use.
4. Using PID temperature control system, the temperature is more accurate (±1°C) (optional).
5. The HS-TFQ smelting equipment is independently developed and manufactured with advanced technical level products for the smelting and casting of gold, silver, copper, etc.
The HS-TFQ series is designed for melting platinum, palladium, Rhodium, gold, silver, copper and other alloys.
6. This equipment apply many foreign famous brands components.
7. It keeps heating while pouring metal liquids at a great condition which enables users to get great quality casting.
-
Smelt Oven Induction Speedy Melting 6kg 8kg 10kg 15kg 20kg Manual Tilting Gold Smelting Furnace
Tilting Melting Furnaces for melting large quantities of metal into ingots or bullions.
These machines are designed for melting large quantities, for example in the gold recycling factory for large capacity melting of 50kg or 100kg per batch.
Hasung TF series – tried and tested in foundries and precious metal refining groups.Our tilting smelting furnaces are mainly used in two areas:
1. for melting down large quantities of metal such as gold, silver or manufacturing metals industry like casting scraps, 15KW, 30KW, and maximum 60KW output and low-frequency tuning means fast melting which enjoys the best results from China – even for large volumes – and excellent through-mixing.
2. for casting large, heavy components after casting in other industries.
The compact and highly cost-effective tilting furnaces from TF6 to TF20 are used in the jewellery industry and in precious metal foundries, are completely new developments. They are equipped with new high performance induction generators that reach the melting point significantly faster and ensure thorough mixing and homogenisation of the molten metals. The ATF30 to ATF100 models, Depending on the model, the capacity ranges from a crucible volume of 30kg to 100kg for gold, mostly for precious metals manufacturing companies.
The TFQ series tilting furnaces are designed for both platinum and gold, all of metals such as platinum, palladium, stainless steel, gold, silver, copper, alloys etc, could be melted in one machine by changing crucibles only.
This type furnaces are great for platinum melting, thus when pouring, machine keeps heating until you almost finish pouring, then pour shuts down automatically when almost finished.
-
Induction Melting Furnace for Gold Platinum Silver Copper Rhodium Palladium
The MU melting unit system is based on the actual needs of the jewelry melting and precious metals refining purpose.
1. HS-MU melting units are independently developed and manufactured with advanced technical level products for the smelting and casting of gold, silver, copper and other alloys.
2. HS-MUQ melting furnaces are equipped with single heating generator but dual use for the smelting and casting of platinum, palladium, stainless steel, gold, silver, copper and other alloys, which can be used by changing crucibles only. Easier and convenient.
-
1kg 2kg Mini Induction Melting Furnace for Gold Silver Copper
The desktop mini induction melting furnace, capacity from 1kg-2kg, which takes 1-2 minutes to melt one batch of metal. It comes in a compact design and can be 24 hours continuously working. Also, this metal furnace is highly environmentally friendly, using 6KW power with 220V single phase which saves a lot of energy to deliver the desired results.
It’s highly recommended for small jewelry factory or jewelry workshop, efficient and long lifetime using. Though it’s small device, it fulfills a great job for users.
Temperature control device is optional for this machine.
Q: What is Electromagnetic Induction?
Electromagnetic Induction was discovered by Michael Faraday in 1831, and James Clerk Maxwell mathematically described it as Faraday’s law of induction.Electromagnetic Induction is a current produced because of voltage production (electromotive force) due to a changing magnetic field.This either happens when a conductor is placed in a moving magnetic field (when using an AC power source) or when a conductor is constantly moving in a stationary magnetic field. As per the setup given below, Michael Faraday arranged a conducting wire attached to a device to measure the voltage across the circuit. When a bar magnet is moved through the coiling, the voltage detector measures the voltage in the circuit.Through his experiment, he discovered that there are certain factors that influence this voltage production. They are:
Number of Coils: The induced voltage is directly proportional to the number of turns/coils of the wire. Greater the number of turns, greater is voltage produced
Changing Magnetic Field: Changing magnetic field affects the induced voltage. This can be done by either moving the magnetic field around the conductor or moving the conductor in the magnetic field.
You may also want to check out these concept related to induction:
Induction – Self Induction and Mutual Induction
Electromagnetism
Magnetic Induction Formula.
Q: What is induction heating?
The Basics Induction starts with a coil of conductive material (for example, copper). As current flows through the coil, a magnetic field in and around the coil is produced. The ability of the of the magnetic field to do work depends on the coil design as well as the amount of current flowing through the coil.
The direction of the magnetic field depends on the direction of current flow, so an alternating current through the coil
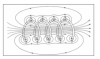
will result in a magnetic field changing in direction at the same rate as the frequency of the alternating current. 60Hz AC current will cause the magnetic field to switch directions 60 times a second. 400kHz AC current will cause the magnetic field to switch 400,000 times a second.When a conductive material, a work piece, is placed in a changing magnetic field (for example, a field generated with AC), voltage will be induced in the work piece (Faraday’s Law). The induced voltage will result in the flow of electrons: current! The current flowing through the work piece will go in the opposite direction as the current in the coil. This means that we can control the frequency of the current in the work piece by controlling the frequency of the current in the
coil.As current flows through a medium, there will be some resistance to the movement of the electrons. This resistance shows up as heat (The Joule Heating Effect). Materials that are more resistant to the flow of electrons will give off more heat as current flows through them, but it is certainly possible to heat highly conductive materials (for example, copper) using an induced current. This phenomenon is critical for inductive heating.What do we need for Induction Heating?All of this tells us that we need two basic things for induction heating to occur:
A changing magnetic field
An electrically conductive material placed into the magnetic field
How does Induction Heating compare to other heating methods?
There are several methods to heat an object without induction. Some of the more common industrial practices include gas furnaces, electric furnaces, and salt baths. These methods all rely on heat transfer to the product from the heat source (burner, heating element, liquid salt) through convection and radiation. Once the surface of the product is heated, the heat transfers through the product with thermal conduction.
Induction heated products are not relying on convection and radiation for the delivery of heat to the product surface. Instead, heat is generated in the surface of the product by the flow of current. The heat from the product surface is then transferred through the product with thermal conduction.
The depth to which heat is generated directly using the induced current depends on something called the electrical reference depth.The electrical reference depth depends greatly on the frequency of the alternating current flowing through the work piece. Higher frequency current will result in a shallower electrical reference depth and a lower frequency current will result in a deeper electrical reference depth. This depth also depends on the electrical and magnetic properties of the work piece.
Electrical Reference Depth of High and Low FrequencyInductotherm Group companies take advantage of these physical and electrical phenomena to customize heating solutions for specific products and applications. The careful control of power, frequency, and coil geometry allows the Inductotherm Group companies to design equipment with high levels of process control and reliability regardless of the application.Induction Melting
For many processes melting is the first step in producing a useful product; induction melting is fast and efficient. By changing the geometry of the induction coil, induction melting furnaces can hold charges that range in size from the volume of a coffee mug to hundreds of tons of molten metal. Further, by adjusting frequency and power, Inductotherm Group companies can process virtually all metals and materials including but not limited to: iron, steel and stainless steel alloys, copper and copper-based alloys, aluminum and silicon. Induction equipment is custom-designed for each application to ensure it is as efficient as possible.A major advantage that is inherent with induction melting is inductive stirring. In an induction furnace, the metal charge material is melted or heated by current generated by an electromagnetic field. When the metal becomes molten, this field also causes the bath to move. This is called inductive stirring. This constant motion naturally mixes the bath producing a more homogeneous mix and assists with alloying. The amount of stirring is determined by the size of the furnace, the power put into the metal, the frequency of the electromagnetic field and the type
count of metal in the furnace. The amount of inductive stirring in any given furnace can be manipulated for special applications if required.Induction Vacuum MeltingBecause induction heating is accomplished using a magnetic field, the work piece (or load) can be physically isolated from the induction coil by refractory or some other non-conducting medium. The magnetic field will pass through this material to induce a voltage in the load contained within. This means that the load or work piece can be heated under vacuum or in a carefully controlled atmosphere. This enables processing of reactive metals (Ti, Al), specialty alloys, silicon, graphite, and other sensitive conductive materials.Induction HeatingUnlike some combustion methods, induction heating is precisely controllable regardless of batch size.
Varying the current, voltage, and frequency through an induction coil results in fine-tuned engineered heating, perfect for precise applications like case hardening, hardening and tempering, annealing and other forms of heat treating. A high level of precision is essential for critical applications like automotive, aerospace, fiber optics, ammunition bonding, wire hardening and tempering of spring wire. Induction heating is well suited for specialty metal applications involving titanium, precious metals, and advanced composites. The precise heating control available with induction is unmatched. Further, using the same heating fundamentals as vacuum crucible heating applications, induction heating can be carried under atmosphere for continuous applications. For example bright annealing of stainless steel tube and pipe.
High Frequency Induction Welding
When induction is delivered using High Frequency (HF) current, even welding is possible. In this application the very shallow electrical reference depths that can be achieved with HF current. In this case a strip of metal is formed continuously, and then passes through a set of precisely engineered rolls, whose sole purpose is to force the formed strip edges together and create the weld. Just before the formed strip reaches the set of rolls, it passes through an induction coil. In this case current flows down along the geometric “vee” created by the strip edges instead of just around the outside of the formed channel. As current flows along the strip edges, they will heat up to a suitable welding temperature (below the melting temperature of the material). When the edges are pressed together, all debris, oxides, and other impurities are forced out to result in a solid state forge weld.
The Future With the coming age of highly engineered materials, alternative energies and the need for empowering developing countries, the unique capabilities of induction offer engineers and designers of the future a fast, efficient, and precise method of heating.